ROTARY KILN
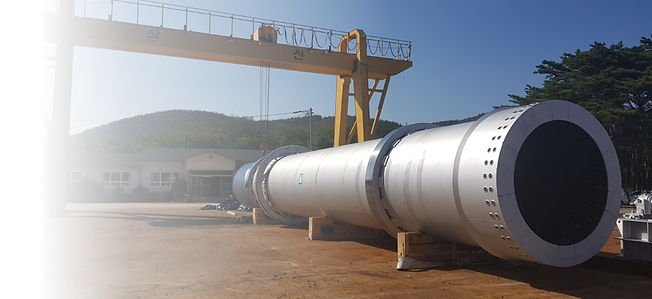


What is Rotary Kiln
The rotary kiln, which is a kind of heating furnace, is a cylindrical high efficiency rotary kiln. it is a steel rotating cylinder furnace in which refractory bricks are attached to inside. It usually put raw material and heated with hot air or flame. It is mainly used to treat chemical materials at high temperature to cause chemical reactions or physical changes.

History of Rotary Kiln
The rotary kiln, originally designed as a British cement kiln in 1877, was born in England, grew up in the United States and was completed in France in the 1900s and has been developed and used in various fields such as ore extraction, metal smelting and waste disposal

How does Rotary Kiln work?
A large cylinder is laid horizontally at a slightly inclined angle, and the raw material is fed from the upper side while rotating the cylinder. The raw material is rotated by gravity along a slight slope, moving downward, outward from below, and heated from inside or outside the cylinder during moving.
The most important technology in the rotary kiln is how to perform the heating temperature, the residence time, the tilting angle, etc. according to the material properties. In particular, maximizing heat transfer between material and heat source to increase thermal efficiency requires skilled design engineers and skilled construction. Rotary Kiln is one of the most important items with long experience and technology.
Samshin offers a customized design system that reflects the needs of customers from small pilot installations to hundreds of tons of large kilns.


Types according to heating method
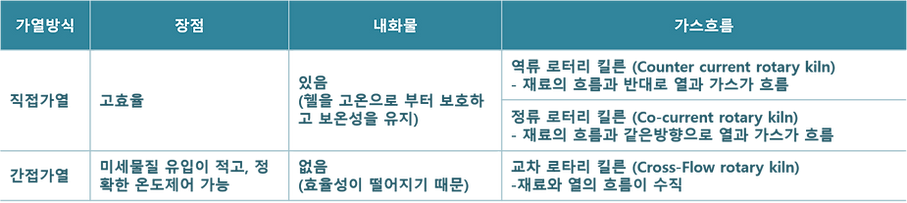
A rotary kiln is classified as a direct-fired or indirect-fired kiln depending on the heating method and can be selected considering which process is more suitable.
The direct-fired has the advantage of high heat efficiency, but the generation of exhaust gas is large, and subsequent treatment is required more. It is usually used in areas where high temperature heating and burning is required, refractory (Castable, Brick, etc.) must be installed to protect inside of the kiln and maintain thermal insulation. Depending on the flow of the process gas, forward flow design or reverse flow design can be considered.
The indirect-fired is a method in which materials are processed in an inert environment without direct contact with the heat source. Since the material is heated by heating the furnace from the outside, the thermal efficiency is lower than the direct heating method. However, the inflow of fine materials can be controlled, and accurate temperature control can be achieved.

DIRECT-FIRED ROTARY KILNS
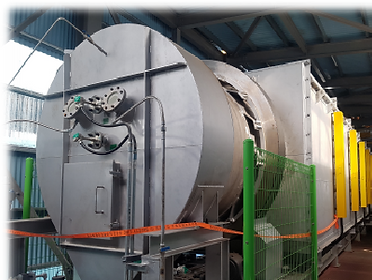
INDIRECT-FIRED ROTARY KILNS

Reverse Flow Rotary Kiln
-
Put material in opposite direction to burner
-
Heat and material move to opposite side
-
High drying position (hot air flows up)
-
Drying as well as heating slowly
-
The higher the efficiency as the material moves, the more heat it receives continuously.
-
Commonly used

Forward Flow Rotary Kiln
-
Wet material is put in burner direction
-
Heat and materials move together
-
Low dry chute position (hot air flows down)
-
Contact with hottest gases in the most humid conditions
-
Rapid heating and evaporation
-
Used when no specific product is needed (waste disposal)

Specification of rotary kiln by various processes

It has been developed for use in cement calcining, but today rotary kilns are used in a variety of thermal processing applications such as mineral extraction, metal smelting, and waste incineration. The most commonly used field is limestone processing for raw material firing to produce cement. In recent years, kiln has been used for rare earth smelting to make ore as raw material. It is also used for the recycling of waste and sewage sludge and fertilizer production. In addition, new applications are being developed.
The basic specifications of the rotary kiln in various processes are shown in the table above. However, this is a basic specification only, and it should be customized after negotiation according to the physical conditions according to the site conditions.

Difference between Kiln and Dryer

KILN
-
Sinter, burn, dry
-
Too much moisture is less efficient
-
Drying takes longer than a dryer
DRYER
-
Low temperature (200 °C ~ 400 °C)
-
Used to remove moisture
-
Mini type available
-
Most of Samshin's kiln projects are dryers
▲ If it is necessary to sinter moisture materials, it is more efficient to add a dryer process before the kiln process

Specification of Samshin's rotary kiln


Rotary Kiln Design Considerations

What is the purpose of using a kiln?
Depending on the intended use, the heating temperature is changed. For calcining purpose, it is usually applied at 1100 ° C to 1300 ° C depending on the properties, and 700 ° C to 900 ° C is applied for combustion purposes.
It also applies 400 ° C at 200 ° C for drying purposes.

What is the size and density of the particles?
If the particles are large or high in density, kiln should be designed more robust because they require more force. However, if the size is larger, the air velocity will drop and the heat efficiency will be lowered. Therefore, it should be designed according to the site conditions and materials.

Have you done special calculations of thermal conductivity and thermal efficiency?
A professional thermal engineering design should be made so that heat can be easily transferred for uniform thermal distribution.Thermal gravimetric analysis (TGA:Thermal Gravimetric Analysis) may be required to determine the change in mass with temperature of the material. Through the TGA it is possible to know what the reaction is at what temperature, which helps to determine the temperature profile. Data collection according to specific heat is also needed to determine the thermal resistance of the material.

Was the chemical structure of the material identified?
It is necessary to understand the chemical reaction that takes place inside the rotary furnace when it is burned to high temperature. Because of the chemical reaction, more heat can be generated than required. Because of the chemical reaction, more heat can be generated than required. Therefore, a design that can resist excessive heat is required. In addition, understanding the chemical composition of the exhaust gas treatment method can also be considered.

Is the heating method selected?
The direct heating method is usually used in areas where high temperature heating and combustion are required, and rectification design or reverse flow design can be considered depending on the gas flow in the process. The indirect heating method is a method in which the material is heated in the high temperature shell by heating the furnace from the outside, so the heat efficiency is lower than the direct heating method, but the inflow of the fine material can be controlled and the temperature can be controlled accurately.

Have you considered heat and air flow?
In direct heating kilns, two types of gas flows can be considered to maximize energy efficiency.
There is a commutation kiln where heat and air flow in the same direction as the raw material, and there is a countercurrent kiln flowing in the opposite direction.
The commutated kiln contacts the coldest material with the hottest gas of the kiln, causing rapid temperature changes and no controlled temperature rise. It is suitable for materials that require rapid temperature changes and do not require specific final products (eg waste treatment kilns).
The countercurrent kiln is heated as the material progressively moves along the ramp and contacts the hottest gas just before discharge. Therefore, less heat is required, fuel consumption is reduced, and thermal efficiency is increased. It is mainly used for sintering in which the material is to be gradually changed in temperature by raising the temperature.
An indirect heating kiln uses a cross flow method in which the material and heat flow are vertical. This can maintain a constant temperature for a long time.


Considerations when selecting a rotary kiln manufacturer

Is it capable of understanding and designing the kiln?
Although it is a simple cylindrical rotary heating furnace, it is the most important facility in the heat treatment process, and it is the rotary kiln which is also the most difficult large facility.
You need to find a competent engineering company capable of precise engineering to properly identify and satisfy your products and processes.

Is a skilled manufacturer capable of ensuring quality?
The use of high-quality raw materials and skilled workmanship make a high-quality rotary kiln longer, extending the service life and preventing costly repairs and unnecessary downtime. Rather than trying to make everything by itself, a company that is based on mutual growth with partners in other specialist fields will become more specialized in every stage of production, and this will result in higher quality products.

Is there long experience and know-how?
The rotary kiln, which has different design conditions according to the material and purpose, is more important than experience and know-how. The construction and installation work from the manufacturer can reduce unnecessary work time in the field, and the calibration of the wheel alignment and the control of the large wheel during the installation process can prevent serious damage during operation. In addition, there are unexpected variables when you work, but you should choose a company that has the expertise to cope with these imminent variables without delay.

Is it possible to produce test equipment?
Rotary kiln is a high-temperature heat treatment system, so it is often the case that a pilot facility is manufactured to meet desired processing capacity and product quality and to develop an effective process. This is a data collection process required to design a rotary furnace of a suitable size in an application field. It is to judge commerciality by evaluating product characteristics by obtaining sample results from a test facility. Other treatment conditions can also be studied.

Quality Warranty and After Service
If you repair or repair a rotary kiln, it will save you time and money by understanding the product quickly and accurately. Also, it is necessary to consider skilled workers in equipment repair, whether it is a technical education and a company that can supply SPARE PART with stability. Rotary Kiln is not a large facility that needs maintenance every year, but it needs maintenance for a long time, and we have to walk firmly for a long time and choose a promising company.

Why should you choose Samshin?

From design to manufacturing
We have many experts in each field, and can guide you through all stages from product design to production management
We provide a complete system through cooperation with various specialized companies for a long time. We are growing together with our partners through quality improvement support based on mutual trust. It is possible not only to provide a single item but also to supply equipment to the manufacturing process.

Perfect collaboration system

Continuous technology development
We will continuously develop technology with company-affiliated research institute and launch new products using high value-added products and core technologies. In addition, it holds numerous industrial machinery patents through continuous and creative research and development.

Quality is the best value
Our unlimited enthusiasm for quality control from production management to delivery date and our unwavering commitment to satisfy our customers' needs by developing differentiated new products through international certification acquisition and capacity building

Customer satisfaction
Through product development, zero defect production, perfect quality control and customer support system through own technology, AS repair can be done until customer is satisfied. It is possible to repair the product even though it is not a product of Samshin.

Vietnam corporation
In February 2016, SamShin of Vietnam was launched, and in March 2019, Vietnam plant was built. A total of 30 employees, including two Korean executives and a local engineer, are stationed in Vietnam's manufacturing plants.

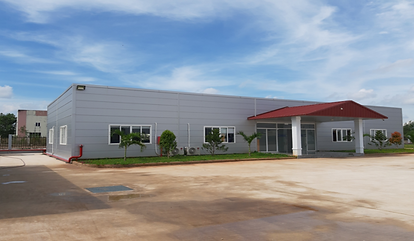
Pictures of Vietnam Samshin

Delivery Performance of Rotary Kiln
WATER BASED SOIL DRYER
2005, REXM
POSCO STS #1 BY PRODUCT CAKE DRYER
2013, POSCO
POSCO STS BY PRODUCT CAKE DRYER
2014, POSCO
STS STEEL MAKING BY PRODUCT NO.2 CAKE DRYER
2018, POSCO
POSCO PosLX ME CO CALCINATION & ROASTING KILN
2018, POSCO